全球船用電池市場呈現(xiàn)高速增長態(tài)勢。根據(jù)行業(yè)報告,2022 年全球電動船市場規(guī)模為 52.6 億美元,預計 2028 年將達 113.5 億美元,復合年增長率 13.7%。其中,船舶磷酸鐵鋰電池市場規(guī)模預計 2025 年將突破 200 億元,系統(tǒng)能量密度已從 100Wh/kg 提升至 160Wh/kg。鋰離子電池因高能量密度(如 NMC 電池比能量達 200-300Wh/kg)和長壽命(循環(huán)次數(shù)超 2000 次),成為主流選擇,占據(jù)全球船用電池市場主導地位。
預計到2032年,歐盟的船用電池市場將從2023年的4.2億美元,增長至超過17億美元,全球需求將超過50億美元。歐洲船用電池市場規(guī)模,2019-2032(十億美元)。鋰離子電池占所有已部署船用儲能的約35%,緊隨其后的是鉛酸電池和燃料電池。應用領域包括為輔助負載和/或推進系統(tǒng)提供能源,適用于從渡輪到游艇的各種船只。
電池應用于三種主要類型的系統(tǒng)中:
半混動:電池作為船舶輔助系統(tǒng)的一部分,以提供混合或全電網(wǎng)。
全混動:電池與船舶的主引擎一同安裝,提供支持或允許船只在短時間內(nèi)以電力驅(qū)動。
全電動:電池是船只的唯一動力來源提供動力。一些全電動游艇使用水翼將船只抬出水面,與排水船相比,能效提高約80%。
船用電池散熱問題是保障船舶電力系統(tǒng)安全、高效運行的關鍵挑戰(zhàn),尤其隨著船舶電動化、智能化發(fā)展,高能量密度電池(如鋰離子電池、固態(tài)電池)的應用普及,散熱需求更加嚴峻。
一、船用電池散熱面臨的核心問題:
1.嚴苛環(huán)境下的散熱需求
- 高功率密度與產(chǎn)熱集中:船用電池(尤其鋰電池)在充放電過程中能量轉(zhuǎn)換效率有限,約 10%-20% 的能量以熱量形式釋放,高倍率充放電(如船舶啟動、急加速)時產(chǎn)熱激增,易導致局部溫度超過 60℃(鋰電池安全閾值),引發(fā)熱失控風險。
- 復雜環(huán)境工況:船舶運行中面臨劇烈振動、鹽霧腐蝕、高濕度(相對濕度>90%)、溫度波動(-20℃~50℃)等環(huán)境,傳統(tǒng)散熱材料(如金屬導熱件)易受腐蝕失效,散熱系統(tǒng)可靠性要求極高。
- 空間與重量限制:船舶電池艙空間緊湊,需在有限體積內(nèi)布置散熱結(jié)構(gòu)(如液冷管路、風冷通道),同時需控制散熱系統(tǒng)重量(避免影響船舶載重與續(xù)航)。
2.散熱不均與安全隱患
- 電池組溫差過大:串聯(lián) / 并聯(lián)電池模塊間散熱效率差異導致溫度不一致(溫差>5℃),加速電池衰減,甚至引發(fā)熱失控連鎖反應。
- 熱管理系統(tǒng)響應滯后:傳統(tǒng)被動散熱(如自然對流)難以應對突發(fā)高負荷工況,主動散熱(如液冷、風冷)依賴傳感器與控制系統(tǒng),若溫控策略不當,易導致散熱不足或過度能耗。
二、關鍵技術挑戰(zhàn):
1.散熱技術與材料適配性
- 被動散熱技術:
- 導熱界面材料(TIM):電池與殼體間需高導熱、耐振動、耐候的材料(如硅基導熱墊片、相變材料 PCM),但鹽霧環(huán)境易導致材料老化、接觸熱阻上升。
- 結(jié)構(gòu)設計:輕量化散熱殼體(如鋁合金、碳纖維復合材料)需兼顧導熱性與耐腐蝕性,海洋環(huán)境中金屬氧化會降低散熱效率。
三、現(xiàn)有解決方案與技術突破:
1.材料層面創(chuàng)新
- 高導熱耐腐蝕材料:
- 散熱殼體:采用表面陽極氧化鋁合金、石墨烯改性復合材料(導熱率>200 W/mK,耐鹽霧壽命>10 年)。
- TIM 升級:使用硅脂 + 氮化硼填料(導熱率>15 W/mK)、有機硅彈性體墊片(耐溫 - 50℃~200℃,抗振動疲勞)。
- 相變材料(PCM)應用:在電池間布置石蠟 / 脂肪酸類 PCM,吸收突發(fā)熱量(潛熱>150 kJ/kg),抑制溫度驟升。
2.散熱結(jié)構(gòu)優(yōu)化
- 一體化液冷設計:
- 微通道液冷板集成于電池托盤,減小流阻與壓降,采用分布式流道設計(如蛇形、叉流)提升均溫性(溫差<3℃)。
- 海水冷卻系統(tǒng)增加離子交換器、防腐涂層(如聚四氟乙烯),降低結(jié)垢與腐蝕風險。
- 風冷與相變耦合:在密閉電池艙內(nèi)結(jié)合熱管(導熱率>10^4 W/mK)與強制風冷,快速導出局部熱點熱量。
3.智能熱管理系統(tǒng)
- 多傳感器融合:部署熱電偶、紅外傳感器、光纖測溫,實時監(jiān)測電池表面與內(nèi)部溫度,結(jié)合 AI 算法預測熱失控風險。
- 能量回收技術:利用船舶發(fā)動機廢熱(50℃~100℃)預熱低溫電池,或通過熱泵回收散熱廢能,提升系統(tǒng)能效(節(jié)能 10%-15%)。
鋰離子電池組在運行中面臨顯著的熱管理挑戰(zhàn):充放電過程中產(chǎn)生的熱量若無法及時均勻散逸,將導致電池組內(nèi)部溫差擴大(通常超過5℃),加速局部老化并可能引發(fā)熱失控風險。尤其在高溫或高倍率工況下,傳統(tǒng)風冷、液冷等外部散熱方式難以有效解決電池單體間的溫度梯度問題。
聚酰亞胺(PI)/氮化硼(BN)納米復合薄膜為解決這一難題提供了創(chuàng)新方案。聚酰亞胺本身具有優(yōu)異的絕緣性和耐高溫性,但導熱系數(shù)較低(約0.2 W/(m·K))。通過引入氮化硼納米片(BNNS)作為導熱填料,可顯著提升材料的熱導率。例如,采用聚多巴胺改性BNNS與聚酰亞胺復合,其導熱系數(shù)可達0.64 W/(m·K),同時保持高絕緣性(擊穿電場強度>200 MV/m)。
該復合薄膜的均熱機制體現(xiàn)在兩方面:1.導熱網(wǎng)絡優(yōu)化:BNNS在聚酰亞胺基體中形成三維導熱路徑,當填料含量超過15wt%時,導熱網(wǎng)絡逐步完善,熱傳導效率顯著提升;2.界面熱阻降低:聚多巴胺改性后的BNNS與聚酰亞胺基體結(jié)合更緊密,減少界面熱阻,進一步改善熱量傳遞效率。廣東晟鵬科技有限公司的SPA-SPK30復合材料為電池均熱問題提供了更高效的解決方案。
該材料通過獨特的各向異性導熱設計:水平熱導率高達20 W/(m·K),可快速沿電池模塊平面方向擴散熱量,減少橫向溫差;垂直熱導率控制在1 W/(m·K),避免熱量在層疊方向過度積聚,優(yōu)化三維熱流分布。實驗數(shù)據(jù)表明,在液冷與風冷混合系統(tǒng)中集成SPA-SPK30后,電池組最大溫差可降至2.5℃以內(nèi),較傳統(tǒng)方案溫差縮減50%。
此外,其耐穿刺性(≥300 N/mm2)和阻燃等級(UL94 V-0)可適配高安全要求的動力電池場景。實際應用效果顯示SPA-SPK30可構(gòu)建多層級熱管理架構(gòu):?SPA-SPK30作為電芯間絕緣導熱層,解決局部熱點問題。
SPA-SPK30用于模組間大面均熱,平衡系統(tǒng)級溫度場。例如,某儲能電池項目中,該方案將溫差從初始的8.2℃壓縮至2.1℃,循環(huán)壽命提升至6000次以上(容量衰減<10%)。同時,SPA-SPK30的輕量化特性(密度1.8 g/cm3)較傳統(tǒng)鋁制散熱件減重40%,進一步優(yōu)化了電池系統(tǒng)能效。
通過材料創(chuàng)新(如PI/BN復合薄膜),鋰電池組均熱問題得以系統(tǒng)性解決,為高能量密度電池的安全應用提供了可靠路徑。
以上部分資料轉(zhuǎn)載網(wǎng)絡平臺,文章僅僅用于交流學習版權歸原作者。如有侵權請告知立刪。
-
電芯
+關注
關注
14文章
779瀏覽量
26508 -
電池
+關注
關注
84文章
11077瀏覽量
134975
發(fā)布評論請先 登錄
PACK電池生產(chǎn)線:從電芯到系統(tǒng)的智能集成之旅
中創(chuàng)新航電池配套海洋工程船
18650電芯自動分選裝盒機:精準分選+高效裝盒,賦能電池生
DIY一款船用鋰電池的思路
汽車電芯的熱管理設計
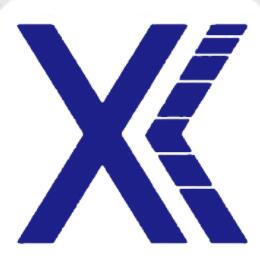
動力電池測試中的直流負載挑戰(zhàn)與應對策略
電池電芯自動分選機:高效精準,賦能電池制造新升級
突破鋰電池運輸堡壘 UN38.3報告打通全球物流
18650電芯自動貼面墊機:革新電芯生產(chǎn)流程的高效利器
鋰電池CE認證要準備哪些資料?
倍加福3D視覺傳感器賦能電池電芯制造
新能源汽車電池三大散熱方案
擴展電池管理系統(tǒng)中電芯監(jiān)控單元的功能
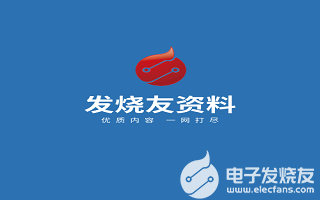
評論